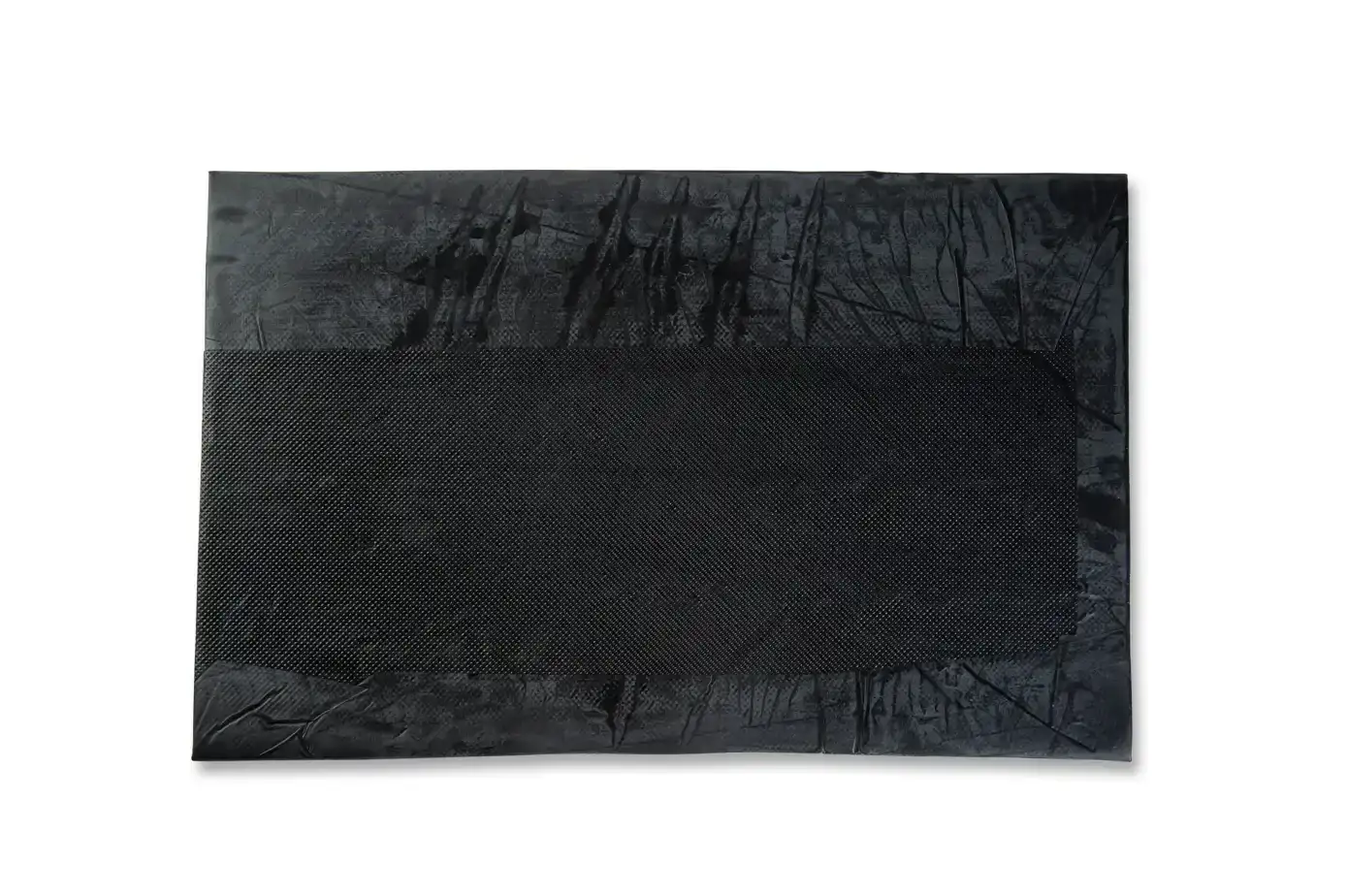
In the complex and dynamic world of the petrochemical industry, few materials hold as much significance as rubber raw materials. These materials, derived from natural and synthetic sources, are integral to the functioning of countless processes and systems within the sector. From sealing components in pipelines to protective linings in storage tanks, rubber raw materials are indispensable, ensuring the safety, efficiency, and reliability of petrochemical operations. This article East explores the multifaceted applications of rubber raw materials in the petrochemical industry, illustrating how they have become the backbone of this vital sector.
The Basics of Rubber Raw Material
Rubber raw material refers to the primary substances used in the manufacture of rubber products. These materials fall into two broad categories: natural rubber and synthetic rubber. Natural rubber is harvested from the latex of rubber trees (Hevea brasiliensis), which are mainly found in Southeast Asia, Africa, and South America. On the other hand, synthetic rubber is produced through chemical processes using petrochemical-derived monomers such as butadiene, styrene, and isoprene.
Rubber raw material is prized for its unique properties, including elasticity, flexibility, durability, and resistance to heat, chemicals, and wear. These characteristics make rubber a versatile material that can be used across a wide range of industries, from automotive to healthcare to consumer goods.
Applications of Rubber Raw Materials in Petrochemical
1. Seals and Gaskets
One of the most critical applications of rubber raw materials in the petrochemical industry is in the production of seals and gaskets. These components are essential for preventing leaks of gases and liquids in machinery, pipelines, and storage tanks. Rubber's inherent flexibility and compressibility allow it to form tight seals between metal surfaces, even under extreme pressure and temperature conditions. This ability to maintain a reliable seal is crucial in the petrochemical industry, where leaks can lead to catastrophic consequences, including environmental contamination and safety hazards.
Rubber seals and gaskets are used in a wide range of equipment, including pumps, valves, compressors, and reactors. They are designed to withstand the harsh conditions typical of petrochemical processes, such as exposure to corrosive chemicals, high temperatures, and intense pressure. The durability and chemical resistance of rubber make it an ideal material for these applications, ensuring long-term performance and reducing the need for frequent maintenance.
2. Hoses and Tubing
Another significant application of rubber raw materials is in the manufacturing of hoses and tubing used to transport various fluids within petrochemical facilities. Rubber hoses and tubing offer the flexibility needed to navigate complex piping systems and can handle the transfer of both gases and liquids, including corrosive substances. This is particularly important in the petrochemical industry, where the safe and efficient transportation of chemicals is paramount.
Rubber hoses and tubing are often reinforced with layers of fabric or metal to enhance their strength and resistance to high pressure. These reinforced rubber products are used in applications ranging from transferring crude oil to transporting refined petrochemical products. The ability to resist abrasion, kinking, and chemical degradation ensures that rubber hoses and tubing can withstand the demanding conditions of petrochemical processes, reducing the risk of leaks and failures.
3. O-Rings
O-rings are perhaps one of the most widely used rubber components in the petrochemical industry. These simple, yet highly effective, sealing elements are used to create a tight seal between two surfaces, preventing the escape of fluids and gases. O-rings made from rubber raw materials are favored for their elasticity, resilience, and ability to maintain their shape under pressure.In the petrochemical industry, O-rings are used in a variety of equipment, including valves, pumps, and hydraulic systems. The selection of the appropriate rubber compound for O-rings is critical, as different compounds offer varying levels of resistance to chemicals, temperature, and wear. For example, fluorocarbon rubber (FKM) O-rings are often used in petrochemical applications due to their excellent resistance to high temperatures and aggressive chemicals.
The reliability of rubber O-rings is essential in ensuring the safe operation of petrochemical processes. A failed O-ring can lead to leaks, which in turn can cause equipment damage, production downtime, and safety hazards. Therefore, the quality and performance of rubber raw materials used in O-rings are of utmost importance in the petrochemical industry.
4. Vibration Dampening
Rubber raw materials play a crucial role in vibration dampening within the petrochemical industry. Machinery and equipment in petrochemical facilities are subject to intense vibrations during operation, which can lead to wear and tear, noise, and potential mechanical failures. Rubber components, such as mounts, pads, and bushings, are used to absorb and dampen these vibrations, prolonging the life of the equipment and improving overall operational efficiency.
The elastomeric properties of rubber make it an ideal material for vibration dampening. Rubber components can be designed to absorb specific frequencies of vibration, reducing the transmission of vibrations to other parts of the machinery. This not only helps protect sensitive equipment but also reduces noise levels in the facility, contributing to a safer and more comfortable working environment.
5. Conveyor Belts
Conveyor belts are a ubiquitous presence in petrochemical facilities, used to transport raw materials, intermediates, and finished products. Rubber raw materials are essential in the production of conveyor belts, providing the necessary durability, flexibility, and resistance to abrasion and chemical exposure.
Rubber conveyor belts are typically reinforced with layers of fabric or steel to enhance their strength and load-bearing capacity. In the petrochemical industry, these belts must be able to withstand the harsh conditions of the production environment, including exposure to oils, chemicals, and extreme temperatures. The resilience of rubber ensures that the conveyor belts can operate reliably over long periods, reducing the risk of breakdowns and production delays.In addition to their durability, rubber conveyor belts offer the flexibility needed to navigate complex conveyor systems. They can be molded and shaped to fit various configurations, making them adaptable to the specific needs of petrochemical facilities. This adaptability, combined with the inherent properties of rubber, makes rubber conveyor belts an indispensable component of the petrochemical industry.
6. Protective Coatings
Rubber raw materials are also used as protective coatings for equipment and infrastructure in the petrochemical industry. Tanks, pipelines, and other equipment exposed to corrosive substances require protection to extend their lifespan and prevent costly repairs or replacements. Rubber coatings provide a barrier that resists chemical attack, abrasion, and environmental degradation.Rubber linings are commonly applied to the interior of storage tanks and pipelines to protect against corrosion and abrasion. These linings are particularly useful in applications where the stored or transported chemicals are highly corrosive, such as acids or alkalis. The rubber lining prevents the chemical from coming into direct contact with the metal surface, reducing the risk of corrosion and leaks.In addition to linings, rubber coatings are also used on external surfaces to protect against environmental factors such as UV radiation, moisture, and temperature fluctuations. These coatings help maintain the integrity of the equipment and infrastructure, ensuring long-term performance and reducing the need for frequent maintenance.
7. Expansion Joints
Expansion joints are another critical application of rubber raw materials in the petrochemical industry. These joints are used to accommodate the thermal expansion and contraction of pipelines and other equipment, preventing damage due to temperature fluctuations. Rubber expansion joints are favored for their flexibility, resilience, and ability to absorb movement and vibration.In petrochemical facilities, pipelines are often exposed to extreme temperatures, which can cause them to expand and contract. Without expansion joints, this thermal movement could lead to stress on the pipelines, resulting in cracks, leaks, or even catastrophic failures. Rubber expansion joints allow for the safe and controlled movement of the pipelines, protecting the integrity of the system and ensuring reliable operation.The design of rubber expansion joints can be customized to meet the specific needs of the petrochemical application. Different rubber compounds can be used to provide resistance to various chemicals, temperatures, and pressures, ensuring that the expansion joints perform effectively under the conditions of the process.
8. Electrical Insulation
Rubber raw materials are widely used as electrical insulation in the petrochemical industry. Electrical components and wiring in petrochemical facilities are often exposed to harsh conditions, including chemicals, moisture, and extreme temperatures. Rubber insulation provides the necessary protection to ensure the safe and reliable operation of electrical systems.Rubber's insulating properties are due to its high dielectric strength and resistance to electrical conductivity. This makes it an ideal material for coating wires, cables, and other electrical components. In addition to its electrical insulating properties, rubber also offers resistance to chemicals and environmental factors, further enhancing the durability and safety of the electrical systems.Rubber insulation is used in a variety of applications, including power distribution systems, control panels, and instrumentation. The use of rubber raw materials in these applications ensures that the electrical systems can operate safely and efficiently, reducing the risk of short circuits, equipment damage, and safety hazards.
Rubber raw materials are truly the backbone of the petrochemical industry, playing a vital role in the safe, efficient, and reliable operation of countless processes and systems. From seals and gaskets to conveyor belts and protective coatings, rubber materials are indispensable in ensuring the integrity and performance of petrochemical facilities.
As the industry continues to evolve, the demand for rubber raw materials will only increase, driven by advances in technology, sustainability initiatives, and the need for ever-greater efficiency and reliability. The continued development and application of rubber materials will be essential in meeting the challenges and opportunities of the future, ensuring that the petrochemical industry remains at the forefront of innovation and progress.
https://www.eastnewmaterial.com/Raw-Rubber
www.eastnewmaterial.com
Chengdu East New Material Co.,Ltd.