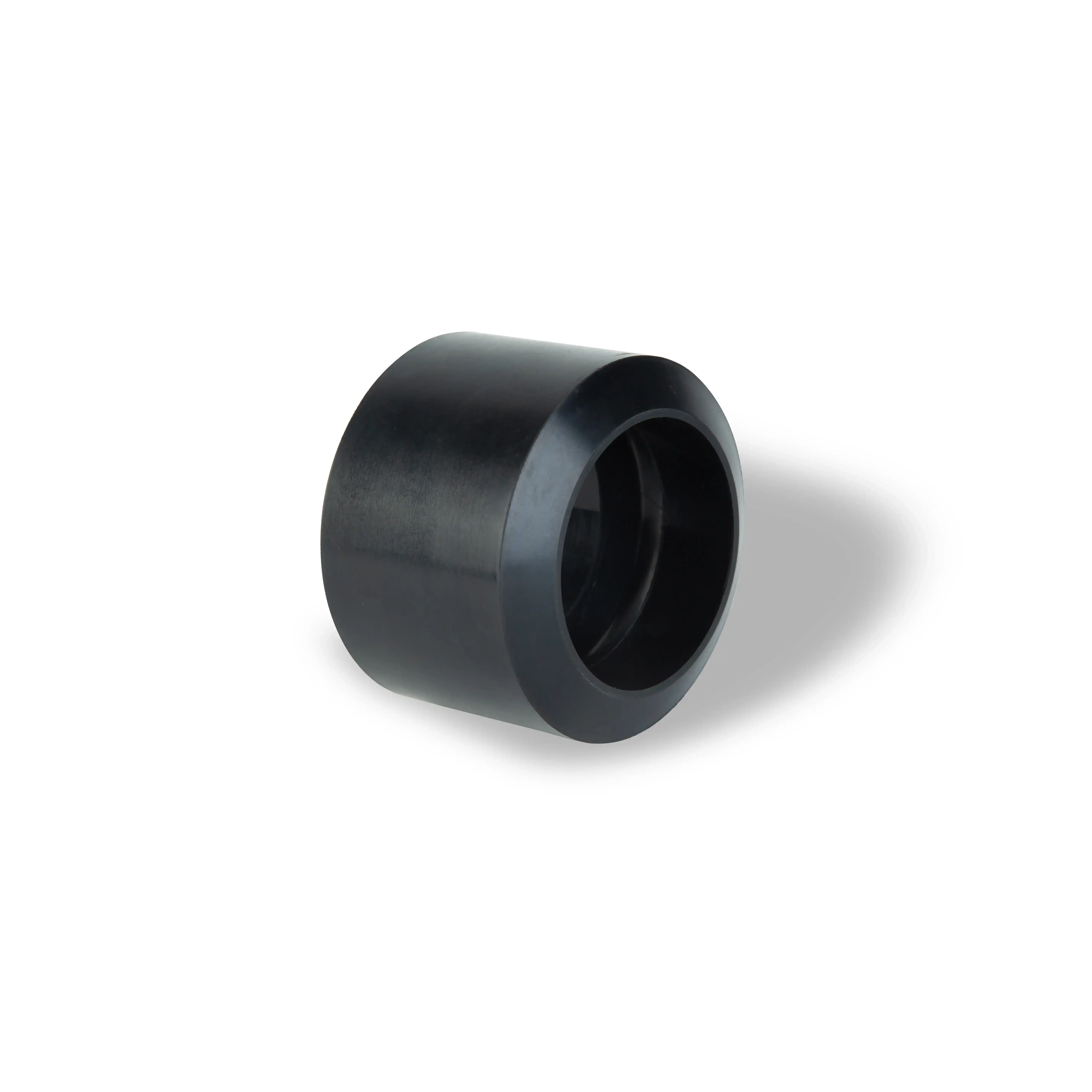
Innovation in materials science has always played a crucial role in shaping our world. As the demand for sustainable solutions grows, scientists and engineers are continuously pushing boundaries to develop eco-friendly materials. In this article, East will explore the concept of dissolvable rubber—an exciting development that promises to revolutionize various industries by providing a sustainable alternative to conventional rubber.
Composition of Dissolvable Rubber
The composition of dissolvable rubber typically involves natural polymers, additives, and other materials to meet desired properties and performance. Here are some commonly used components:
Natural Polymers
Dissolvable rubber is often based on natural polymers derived from renewable sources. These can include cellulose, starch, chitin, or other biopolymers. These natural polymers serve as the primary component and provide the structure and biodegradability of the material.
Cross-linkers
Cross-linkers are additives that help strengthen the structure of dissolvable rubber. They promote the formation of chemical bonds between polymer chains, increasing the material’s mechanical properties and stability. Common cross-linkers include glyoxal, glutaraldehyde, or other similar compounds.
Plasticizers
Plasticizers are added to improve the flexibility and elasticity of the dissolvable rubber. They help reduce brittleness and enhance the material’s ability to withstand deformation without breaking. Examples of plasticizers commonly used in dissolvable rubber include glycerol, sorbitol, or other compatible organic compounds.
Fillers
Fillers are added to modify the physical properties of dissolvable rubber, such as its strength, hardness, or thermal conductivity. Fillers can include materials such as silica, carbon black, or other reinforcing agents. These fillers enhance the material’s mechanical properties and can also improve its processability during manufacturing.
Additives
Other additives may be incorporated to enhance specific properties or functionalities of dissolvable rubber. These can include antioxidants, UV stabilizers, antimicrobial agents, or colorants. These additives can address issues such as degradation due to environmental exposure or add aesthetic appeal to the material.
Production Process of Dissolvable Rubber
The production process of dissolvable rubber typically involves the following steps:
Raw Material Selection
Choose suitable natural polymers, such as cellulose, starch, or chitin, as the base for the dissolvable rubber.
Mixing and Blending
Mix the selected natural polymers with water and other additives, such as cross-linkers, plasticizers, and fillers, to achieve the desired properties and consistency.
Shaping and Forming
Use techniques like extrusion or molding to shape the mixed material into the desired form, such as sheets, films, or specific product components.
Cross-Linking
If required, initiate the cross-linking process to strengthen the material and improve its stability. This can be achieved through heat, chemical agents, or irradiation.
Curing and Drying
Cure the material to enhance its final properties, such as hardness or resistance to environmental factors. This may involve exposing the material to specific temperatures or allowing it to dry naturally.
Quality Control
Implement quality control measures throughout the production process to ensure the consistency and performance of the dissolvable rubber. This may include testing the material for mechanical properties, biodegradability, and chemical stability.
Packaging and Distribution
Package the final product appropriately for storage and distribution.
Dissolvable rubber represents a remarkable advancement in the quest for sustainable materials. Its ability to biodegrade under specific conditions while maintaining similar performance characteristics to rubber opens a realm of possibilities for various industries. By embracing these innovative solutions, we can inspire positive and contribute to a world thrives on sustainability.
https://www.eastnewmaterial.com/Dissolvable-Rubbers.html
Leah
annikahan@wsmaterial.com