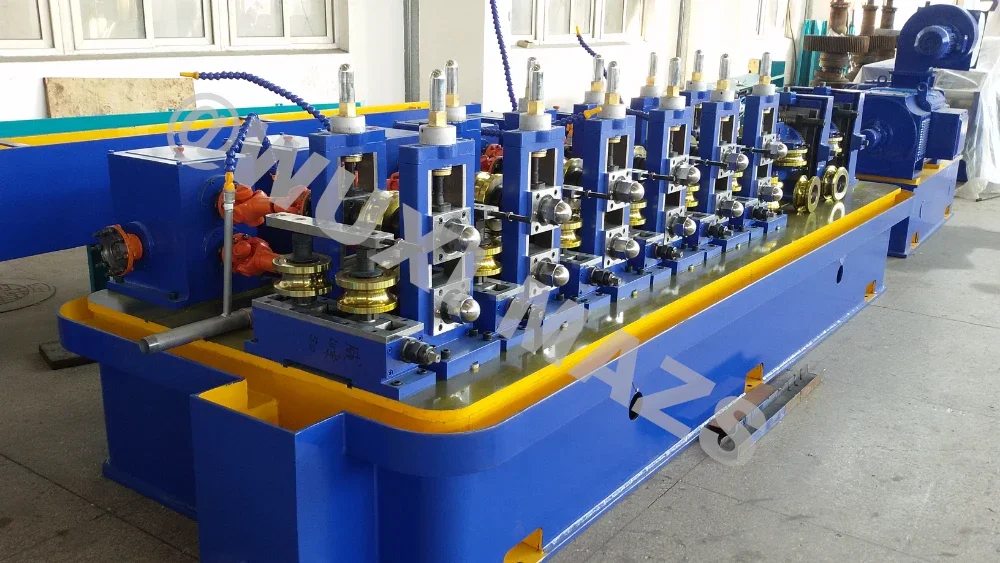
In the world of modern manufacturing, the demand for high-quality, efficient, and versatile equipment has never been higher. One such piece of machinery that has become indispensable in the production of metal tubing is the HF tube mill, short for High-Frequency tube mill, this advanced technology has revolutionized the way metal tubes are made, offering unparalleled precision, speed, and flexibility. Whether for automotive, construction, or industrial applications, HF tube mills have become the go-to solution for producing a wide variety of tubular products. In this article, Mazs delves into the intricacies of HF tube mills, exploring their working principles and advantages in the manufacturing industry.
What is an HF Tube Mill?
An HF tube mill is a specialized piece of equipment used in manufacturing to produce metal tubes from strips of material. The "HF" stands for "High Frequency," referring to the electrical current used in welding. The tube mill transforms flat metal strips, known as skelp, into a continuous length of tube through a series of processes, including forming, welding, sizing, and cutting.
The core component that sets HF tube mills apart from other types of tube mills is their use of high-frequency electric resistance welding (ERW). This method employs high-frequency electrical currents to generate localized heat, allowing the edges of the metal strip to be welded together as they are formed into a tubular shape. This process is highly efficient, enabling the production of strong, consistent welds at high speeds, which is essential for large-scale manufacturing operations.
HF tube mills can produce tubes of various sizes, thicknesses, and materials, including carbon steel, stainless steel, and non-ferrous metals such as aluminum and copper. This versatility makes them suitable for a wide range of applications, from automotive components and construction materials to furniture frames and industrial piping systems.
The Working Principles of an HF Tube Mill
Understanding the working principles of an HF tube mill requires a closer look at the key stages involved in the tube manufacturing process. While the specifics can vary depending on the design and application of the mill, the general workflow typically includes the following steps:
Uncoiling and Leveling
The process begins with large coils of flat metal strips, which are loaded onto an uncoiler. The uncoiler feeds the strips into a series of rollers that straighten and level the material, ensuring it is flat and free of any distortions or imperfections. This step is crucial for ensuring the quality and consistency of the final product. Proper leveling of the strip prevents defects such as bends or waves in the finished tube, which can compromise the tube's structural integrity and performance.
Forming
After leveling, the flat strip enters the forming section of the HF tube mill. Here, a series of forming rolls gradually bend the strip into a round or square shape, depending on the desired profile of the tube. The forming rolls are carefully designed to provide precise control over the shaping process, ensuring that the tube's dimensions and geometry are consistent throughout its length. The accuracy of the forming process is essential for achieving the desired final product specifications and for maintaining the alignment of the strip edges for welding.
High-Frequency Welding
Once the strip has been formed into the desired shape, it passes through the welding section of the mill. In this section, high-frequency electrical currents are applied to the edges of the strip, generating intense localized heat that causes the metal to fuse together. The high-frequency welding process is extremely efficient, allowing for continuous production at high speeds with minimal downtime. This method also produces strong, high-quality welds that are virtually indistinguishable from the base material, ensuring the structural integrity of the finished tube. The high-frequency welding process is controlled by precise power settings and advanced feedback mechanisms to ensure consistent weld quality and to prevent issues such as burn-through or inadequate fusion.
Sizing and Straightening
After welding, the tube passes through a series of sizing rolls that refine its dimensions and ensure it meets the required specifications. This step is crucial for achieving the desired outer diameter, wall thickness, and shape of the tube. Additionally, straightening rolls are used to correct any minor deviations in the tube's alignment, ensuring that it is perfectly straight and free of any bends or twists. The sizing and straightening process also helps to relieve any residual stresses in the material caused by the forming and welding processes, ensuring the tube remains dimensionally stable over time.
Cutting and Finishing
Once the tube has been formed, welded, sized, and straightened, it is cut to the desired length using a flying cutoff saw or a rotary cutoff machine. The cutting process must be precise and efficient to minimize waste and ensure the final product meets the required specifications. After cutting, the tubes may undergo additional finishing processes, such as deburring, polishing, or coating, to enhance their appearance and performance. Finishing processes can also include heat treatment or surface treatments to improve the tube's mechanical properties or to protect it against corrosion and wear.
The Advantages of Using HF Tube Mills in Modern Manufacturing
The HF tube mill offers several key advantages that make it a preferred choice for manufacturers around the world. These advantages include:
High Production Speed
One of the most significant benefits of HF tube mills is their ability to operate at high speeds. The high-frequency welding process allows for continuous production with minimal downtime, enabling manufacturers to produce large quantities of tubes quickly and efficiently. This high production speed is particularly beneficial for industries with high demand for tubular products, such as automotive, construction, and oil and gas. The ability to maintain high production rates without sacrificing quality makes HF tube mills a cost-effective solution for mass production environments.
Superior Weld Quality
The high-frequency welding process used in HF tube mills produces strong, consistent welds that are virtually indistinguishable from the base material. This superior weld quality ensures that the finished tubes have excellent structural integrity and are free of defects, making them suitable for critical applications where safety and reliability are paramount. The welding process is also highly controllable, allowing for adjustments in weld parameters to accommodate different materials and thicknesses, ensuring optimal weld quality across a range of applications.
Versatility in Material and Size
HF tube mills are capable of processing a wide range of materials, including carbon steel, stainless steel, and non-ferrous metals such as aluminum and copper. Additionally, these mills can produce tubes in various sizes, shapes, and thicknesses, offering manufacturers the flexibility to meet diverse customer requirements and market demands. The ability to produce a wide variety of tube profiles allows manufacturers to serve multiple markets with a single piece of equipment, increasing their operational flexibility and reducing capital investment costs.
Precision and Consistency
The advanced forming and welding technology used in HF tube mills allows for precise control over the tube's dimensions and geometry, ensuring consistent quality and performance. This precision is particularly important for applications where tight tolerances are required, such as automotive components, structural tubing, and hydraulic systems. The high degree of control provided by modern HF tube mills also reduces the need for post-production inspection and rework, further enhancing manufacturing efficiency and reducing costs.
Energy Efficiency
The high-frequency welding process used in HF tube mills is highly energy-efficient, reducing overall energy consumption and operating costs. This efficiency is achieved by generating heat only in the area where it is needed (the weld seam), minimizing energy waste and reducing the mill's environmental footprint. The energy savings offered by HF tube mills are particularly important in today's manufacturing environment, where sustainability and cost control are key priorities for many companies.
Low Maintenance Requirements
HF tube mills are designed for durability and reliability, with low maintenance requirements and long service life. The robust construction and high-quality components used in these mills ensure that they can withstand the rigors of continuous operation, reducing downtime and maintenance costs. The reduced maintenance requirements of HF tube mills also translate into lower overall operational costs and increased uptime, making them a highly cost-effective solution for high-volume tube production.
The HF tube mill has become an essential tool in modern manufacturing, offering a versatile, efficient, and high-quality solution for producing metal tubes. With its ability to operate at high speeds, produce superior welds, and handle a wide range of materials and sizes, the HF tube mill is well-suited to meet the diverse needs of industries around the world. As technology continues to evolve and new opportunities emerge, the HF tube mill is poised to play an even more significant role in the future of manufacturing, driving innovation and enabling the production of high-performance products that meet the demands of an ever-changing market. Whether you are in the automotive, construction, oil and gas, or any other industry, the HF tube mill offers the reliability, precision, and efficiency needed to succeed in today's competitive landscape.
https://www.mazsmachine.com/MA76E-127-HF-Tube-Mill.html
www.mazsmachine.com
WUXI MAZS MACHINERY GROUP