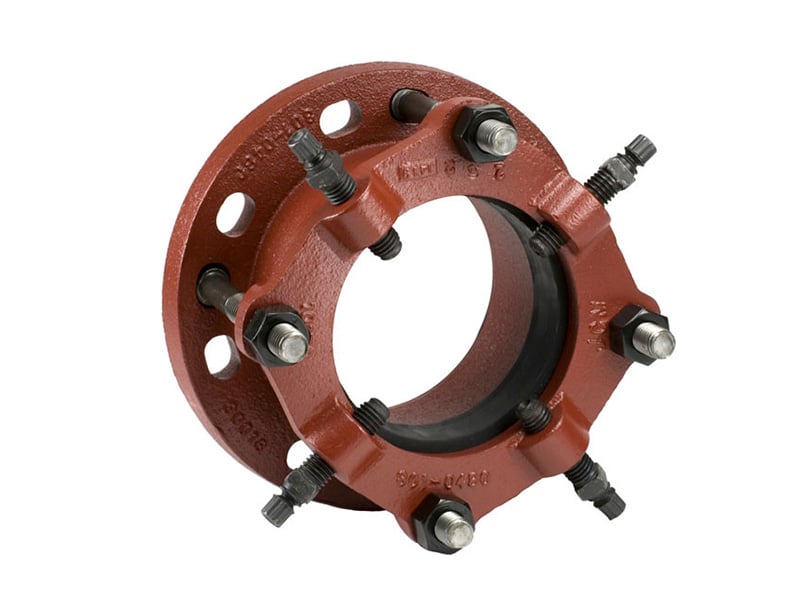
In the intricate network of piping systems across industries, the role of mechanical joints is paramount, shaping the efficiency, reliability, and safety of fluid transport. This exploration aims to delve into the multifaceted purpose of mechanical joints in pipes, unraveling the complexities that make them indispensable in diverse applications.
1. Ensuring Leak-Free Connections:
One of the primary purposes of mechanical joints in pipes is to establish leak-free connections. Whether in water distribution, chemical processing, or industrial applications, the robust design of mechanical joints ensures a tight seal, preventing fluid leakage that could compromise the integrity of the system and pose safety hazards.
2. Facilitating Ease of Installation and Maintenance:
Mechanical joints contribute to the ease of installation and maintenance in piping systems. Their design allows for quick and efficient assembly, reducing downtime during installation or repairs. This is particularly crucial in industries where minimizing operational disruptions is a priority.
3. Accommodating Thermal Expansion and Contraction:
Pipes are subjected to temperature variations, leading to thermal expansion and contraction. Mechanical joints are engineered to accommodate these fluctuations without compromising the structural integrity of the system. This feature is essential in applications where pipes are exposed to varying environmental conditions.
4. Adapting to Different Pipe Materials:
Piping systems utilize a variety of materials based on the requirements of the application. Mechanical joints are designed to accommodate different pipe materials, including metals, plastics, and composites. This adaptability enhances the versatility of mechanical joints across industries with diverse material requirements.
5. Providing Structural Support:
In addition to their sealing capabilities, mechanical joints offer structural support to the piping system. They help distribute loads, absorb vibrations, and ensure stability, especially in applications where pipes are subject to external forces or dynamic conditions. This structural support contributes to the longevity and reliability of the entire system.
6. Addressing Misalignments and Offset:
During installation or over time, pipes may experience misalignments or offsets. Mechanical joints are engineered to compensate for these deviations, ensuring a secure and aligned connection. This adaptability is crucial in complex piping systems where precise alignment is challenging to maintain.
7. Enhancing System Flexibility:
The purpose of mechanical joints extends to enhancing the overall flexibility of piping systems. This flexibility allows for adjustments and modifications to the system layout, accommodating changes in operational requirements or expansions without the need for extensive reconfiguration.
8. Meeting Industry Standards and Regulations:
Mechanical joints in piping systems are designed and manufactured to meet industry standards and regulations. Compliance with these standards ensures that the joints adhere to safety, performance, and quality criteria, providing assurance to engineers, operators, and regulatory bodies.
Conclusion:
In the intricate tapestry of fluid dynamics, the purpose of mechanical joints in pipes emerges as a linchpin, influencing the seamless operation and longevity of diverse systems. This exploration has unveiled the significance of mechanical joints in ensuring leak-free connections, facilitating ease of installation and maintenance, accommodating thermal fluctuations, adapting to various pipe materials, providing structural support, addressing misalignments, enhancing system flexibility, and meeting industry standards. As industries evolve, the role of mechanical joints remains pivotal, forging the backbone of resilient and efficient piping systems across the globe.