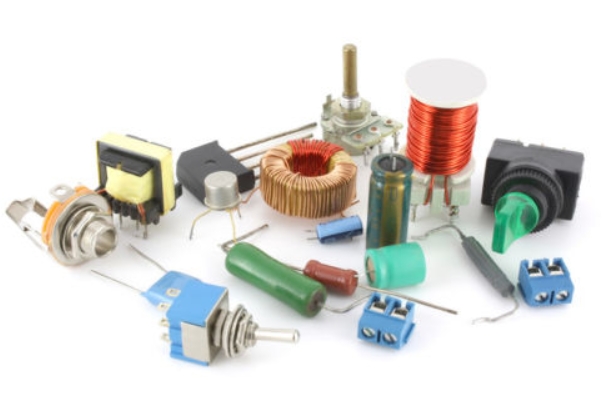
In today's fast-paced technological world, electronic components play a crucial role in various industries. However, the presence of defective components can lead to significant issues, ranging from product failures to safety hazards. Therefore, it is essential to understand how to identify defective electronic components to ensure the reliability and performance of electronic devices. In this blog post, we will delve into the depths of this topic, exploring the methods and techniques used to detect and prevent the use of defective electronic components.
- Understanding the Impact of Defective Electronic Components:
Defective electronic components can have severe consequences, including system failures, reduced product lifespan, and potential safety hazards. It is crucial to comprehend the potential risks associated with using faulty components, as they can lead to financial losses, damage to reputation, and even endanger human lives. By understanding the impact, individuals and businesses can prioritize quality control measures and implement effective strategies to mitigate risks. - Visual Inspection Techniques:
Visual inspection is often the first step in identifying defective electronic components. This technique involves a thorough examination of the components for any visible defects, such as physical damage, discoloration, or irregularities in shape or size. Additionally, advanced inspection tools, such as magnifying lenses and microscopes, can aid in detecting minute defects that may not be visible to the naked eye. Visual inspection serves as a preliminary screening method to identify potential issues before further testing. - Electrical Testing and Analysis:
Electrical testing is a critical step in identifying defective electronic components. Various testing methods, such as continuity testing, voltage testing, and resistance testing, can be employed to assess the functionality and performance of components. Additionally, advanced techniques like in-circuit testing and functional testing can provide a comprehensive evaluation of the components' behavior under specific operating conditions. These tests help detect anomalies, such as short circuits, open circuits, or incorrect values, indicating potential defects. - Environmental Stress Testing:
Environmental stress testing involves subjecting electronic components to extreme conditions, such as temperature variations, humidity, vibration, and electrical surges. By simulating real-world scenarios, this testing helps identify potential weaknesses or defects that may arise due to environmental factors. Components that fail to withstand these stress tests may be considered defective and should be replaced or rectified to ensure long-term reliability. - Collaboration with Suppliers and Quality Assurance:
To ensure the procurement of non-defective electronic components, establishing strong relationships with reliable suppliers is crucial. Collaborating with suppliers who prioritize quality control measures, adhere to industry standards, and provide comprehensive documentation can significantly reduce the risk of receiving defective components. Additionally, implementing robust quality assurance processes within your organization, such as incoming inspections and supplier audits, can further enhance the detection and prevention of defective components.
Conclusion:
Identifying defective electronic components is a critical aspect of ensuring the reliability, performance, and safety of electronic devices across various industries. By employing visual inspection techniques, electrical testing and analysis, environmental stress testing, and fostering strong supplier relationships, individuals and businesses can effectively detect and prevent the use of defective components. Prioritizing quality control measures and staying updated with the latest industry advancements will help maintain a competitive edge while ensuring the delivery of high-quality electronic products.