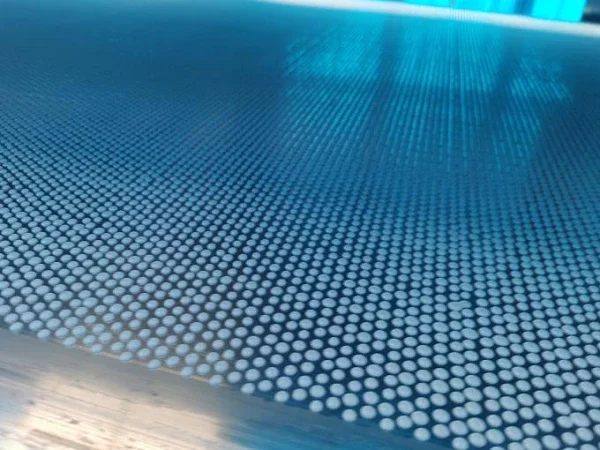
As key equipment in compound fertilizer production, the NPK fertilizer granulator plays a vital role in the fertilizer industry. NPK fertilizer consists primarily of three essential nutrients: nitrogen (N), phosphorus (P), and potassium (K), all of which are crucial for plant growth. To meet the demand for efficient and balanced nutrient supply in agricultural production, NPK fertilizer production requires extremely high precision and efficiency. The NPK fertilizer granulator efficiently and consistently transforms these nutrients into easy-to-use granular fertilizers, supporting large-scale agricultural applications. This article Little Sky provides a detailed introduction to the production process and practical applications of NPK fertilizer granulators, offering insight into this critical piece of equipment.
Production Process of NPK Fertilizer Granulators
The production process of NPK fertilizer granulators is highly automated, from the heating and melting of raw materials to the cooling and granulation of the final fertilizer. This ensures high efficiency in the production of NPK fertilizers and consistent product quality.
Raw Material Melting and Mixing
The first step in NPK fertilizer production is heating the raw materials to a molten state. Typically, a mixing furnace is used to combine nitrogen, phosphorus, potassium, and other additives. These materials are heated to a specific temperature to ensure they are fully melted. The quality and uniformity of the molten mixture significantly affect the shape and strength of the final granules. Thus, during the heating process, both temperature and mixing speed must be carefully controlled to ensure all components are thoroughly integrated. In the production of NPK compound fertilizers, controlling the melting temperature is particularly important. Different NPK ratios require precise temperature ranges. Excessive heat may cause decomposition of some components, while insufficient heat can affect fluidity and hinder the granulation process.
Spraying and Steel Belt Cooling
Once the raw materials are melted, they are sprayed evenly onto the surface of a high-speed steel belt using a molten material spraying system. The cooling speed and temperature control of the steel belt are critical at this stage. The cooling system ensures that the belt temperature is maintained within a specific range, enabling rapid absorption of the heat from the molten materials. This process transforms the molten material into solid granules within seconds. The uniformity of cooling on the steel belt determines the final shape and quality of the granules. Proper temperature management ensures that the granules cool at an optimal rate, preventing brittleness or incomplete formation.
Granule Threshing and Collection
After cooling and forming, the granules enter the threshing stage. The threshing system, using mechanical vibration or other methods, separates the solidified granules from the steel belt. It is important to ensure that the granules are not exposed to excessive mechanical force to avoid cracking or damage. The threshed granules are then sent to a screening device to separate finished granules from those that do not meet specifications. Unqualified granules are recycled and reprocessed, while the finished granules proceed to the packaging stage.
Practical Applications of NPK Fertilizer Granulators
The NPK fertilizer granulator is widely used in various industries, including fertilizer production companies, agricultural planting bases, and chemical plants. Given the critical role of NPK fertilizers in global agriculture, there is a significant demand for this equipment worldwide.
Application in Agricultural Planting Bases
In large-scale farming, NPK compound fertilizers are a key means of increasing crop yield and quality. The NPK fertilizer granulator can produce fertilizers with different nutrient ratios, tailored to the needs of specific crops at different growth stages. This allows precise fertilization, improving yields. For instance, in rice cultivation, the requirements for nitrogen, phosphorus, and potassium vary at different growth stages. The NPK fertilizer granulator can produce fertilizer formulas designed to meet the nutrient needs of rice at each stage, ensuring accurate and efficient fertilization.
Application in Fertilizer Production Companies
In fertilizer production companies, the NPK fertilizer granulator is the core equipment for improving production efficiency and maintaining product quality. Through efficient granulation processes, companies can produce large volumes of high-quality compound fertilizers in a short time to meet market demand. The use of automated equipment also reduces labor costs and improves overall operational efficiency. Moreover, many fertilizer companies have enhanced their product competitiveness and expanded their market presence, both domestically and internationally, by investing in modern NPK fertilizer granulation technology.
As critical equipment in the production of compound fertilizers, NPK fertilizer granulators not only significantly improve production efficiency and product quality but also contribute to the sustainable development of modern agriculture. As agricultural technology advances and fertilizer demand diversifies, the role of the NPK fertilizer granulator will become even more important in the future.
https://www.th-littlesky.com/Compound-Fertilizer-Granulator-Supply.html
www.th-littlesky.com
Little Sky Mechanical Engineering Thailand Co.,Ltd